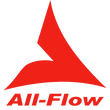(2)_edited.png)
Vacuum Steam Jet Ejector System
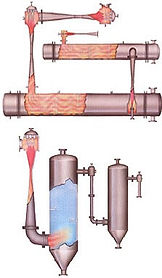
"JOYAM" Steam jet ejector system having no moving parts works on the principle of converting the pressure energy of a motivating fluid to velocity energy in order to entrain the suction fluid. Vacuum is created, air or gas is entrained and mixture or gas and steam enters the venturi diffuser where its velocity energy is converted into pressure, sufficient to discharge against a predetermined back pressure. Designs upto 0.05 torr.
​
In certain process applications the demand for air / vapour to be evacuated, is fluctuating as the process parameters varies with time. With single vacuum pump this leads to the fluctuation of vacuum. Hence constant vacuum cannot be maintained in the system. Which may affect the quality of the product or the performance of the system connected.
​
Joyam has developed a unique vacuum pool, by combination of two vacuum pumps and a reservoir tank, which fulfills fluctuating demand keeping the vacuum virtually constant. The system is also designed for unique capacity control to save on electrical energy. The other important feature of the system is re circulation of sealing liquid, which saves on the cost of sealing liquid and reduces the load on effluent treatment.
​
Two or more vacuum pumps operate in a parallel operation through a common reservoir. During operation One pump runs continuously and the second pump is switched on & off depending upon the process demand and keeping vacuum virtually constant to the set value.
Material Of Construction :
As Per Process Requirement
Salient Features:
Meets the fluctuating process demand keeping the vacuum constant. Automatic capacity control saves considerably on electrical energy.
Re circulation of sealing liquid with inter cooling saves the cost.
Capacity :
Tailor-made units can be made as per the process parameters.

WHY PARTNER WITH ALLFLOW?
Specialize in alternative fuel firing systems
Allflow has a vast knowledge and understanding of fuel-fired systems process knowledge, feasibility studies and technical solutions, such as receiving, handling, sorting, sizing, storing, transporting, feeding and burning.
Experienced
Allflow has commissioned more than 30 Alternate Fuel Firing Systems in cement plants in India during the period of 2009-20.
Engineering Design
Each system is individually designed by Allflow based on the norms of PCB and customer’s input.
Customer Service
Allflow is fully equipped with an experienced operational team to assist the customer to fire the secondary fuel inefficient and safer way.